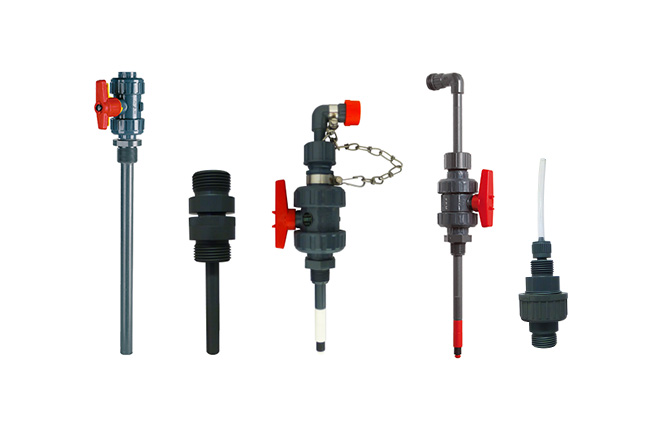
Injection nozzles
Injecting the transported chemicals
The injection nozzle is a fitting with which the dosing medium is introduced into a pressurised system. A non-return valve with a spring-loaded ball (type R) or a valve hose (type S) ensures that under conditions of normal dosing operation and with process-related shut down times, no process medium can flow backwards into the dosing pump. Injection nozzles should be fitted with a shutoff valve wherever possible. This means that the dosing system (inc. non-return valve) can be separated from the pressurised system (e.g. for maintenance). The shutoff valve can be closed during longer downtimes, as the leak-free status of the non-return valve can be compromised through impurities or wear.
Features & Benefits
- Flow capacity 70 – 2600 l/h
- Opening pressure 0.2 – 1.1 bar
- System pressure PN10 or PN16 (special versions up to PN160)
- Type S: a pre-tensioned hose effects very fine spraying of the chemical during the dosing stroke
- Type SAH: Dismantling of the injection pipe under system pressure possible
- Type SKD: self-cleaning by constantly-moving injection hose in the main flow
- The injection pipe enables the spraying of the dosing chemical in the centre of the pipe line, and ensures good mixing
- The non-return valve (type R and S) prevents fluids from the pressurised system from flowing back into the dosing pump
- A shutoff valve enables the dosing system to separate from the pressurised system and provides a secure shutoff during longer downtimes
- A cooling pipe enables the emission of heat, if dosing is to be performed via a plastic dosing line in a system with high temperatures
- Different transmissions from the injection nozzle to the dosing line possible e.g. hose, a rigid line or via a flange